What is Porosity in Welding: Secret Factors and Their Impact on Weld Quality
Porosity in Welding: Identifying Common Issues and Implementing Ideal Practices for Avoidance
Porosity in welding is a pervasive problem that commonly goes undetected up until it triggers considerable issues with the stability of welds. In this discussion, we will explore the key factors adding to porosity development, examine its harmful effects on weld efficiency, and discuss the finest methods that can be embraced to decrease porosity event in welding processes.
Usual Root Causes Of Porosity
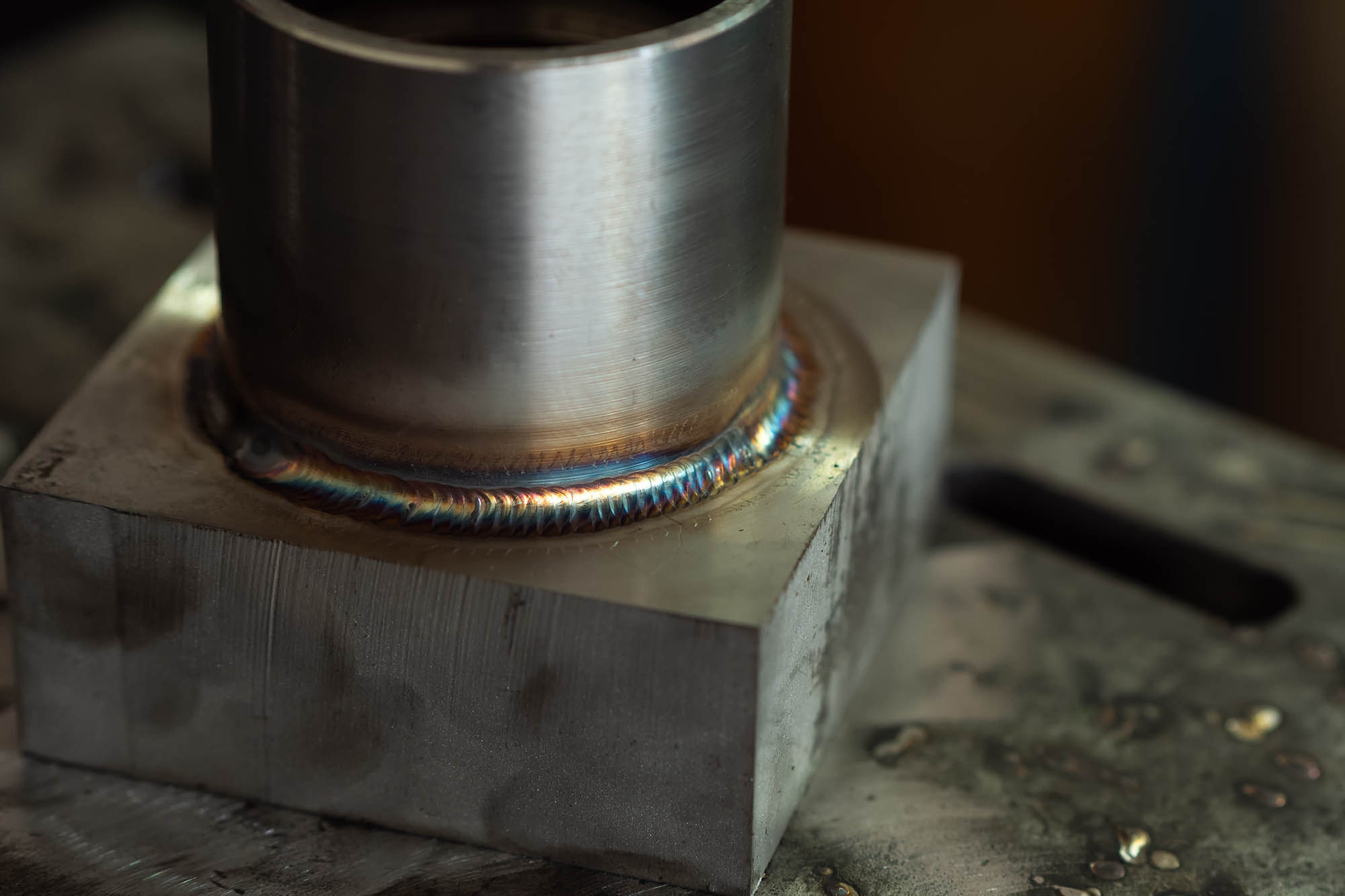
An additional regular wrongdoer behind porosity is the presence of contaminants on the surface area of the base steel, such as oil, oil, or rust. When these pollutants are not properly removed before welding, they can vaporize and end up being caught in the weld, creating issues. Additionally, utilizing unclean or damp filler products can present contaminations right into the weld, adding to porosity issues. To mitigate these usual root causes of porosity, detailed cleansing of base steels, correct protecting gas option, and adherence to optimum welding criteria are essential practices in achieving high-quality, porosity-free welds.
Influence of Porosity on Weld High Quality

The visibility of porosity in welding can considerably endanger the structural stability and mechanical properties of welded joints. Porosity develops voids within the weld metal, damaging its overall stamina and load-bearing ability.
One of the primary repercussions of porosity is a decline in the weld's ductility and toughness. Welds with high porosity levels have a tendency to show lower effect toughness and reduced ability to warp plastically prior to fracturing. This can be specifically worrying in applications where the bonded components go through dynamic or cyclic loading conditions. In addition, porosity can impede the weld's ability to efficiently transfer forces, causing early weld failing and prospective safety and security threats in critical frameworks.
Ideal Practices for Porosity Prevention
To boost the structural honesty and quality of welded joints, what details actions can be executed to reduce the event of porosity throughout the welding procedure? Porosity prevention in welding is essential to guarantee the stability and strength of the final weld. One reliable method is proper cleansing of the base metal, getting rid of any type of contaminants such as corrosion, oil, paint, or moisture that can cause gas entrapment. Making sure that check the welding equipment remains in good problem, with clean consumables and proper gas flow prices, can also dramatically minimize porosity. Additionally, maintaining a secure arc and controlling the welding specifications, such as voltage, current, and travel rate, helps produce a consistent weld pool that decreases the risk of gas entrapment. Utilizing the appropriate welding strategy for the particular product being bonded, such as adjusting the welding angle and weapon placement, can further stop porosity. Normal evaluation of welds and instant removal see it here of any type of concerns identified during the welding process are crucial practices to stop porosity and generate high-quality welds.
Value of Appropriate Welding Techniques
Implementing proper welding strategies is extremely important in making certain the structural integrity and top quality of bonded joints, developing upon the foundation of effective porosity avoidance procedures. Welding techniques straight influence the general toughness and resilience of the welded framework. One crucial aspect of correct welding methods is maintaining the correct warmth input. Excessive warmth can cause enhanced porosity as a result of the entrapment of gases in the weld swimming pool. Alternatively, inadequate heat might result in insufficient fusion, developing potential powerlessness in the joint. Furthermore, making use of the proper welding specifications, such as voltage, current, and take a trip speed, is vital for achieving audio welds with minimal porosity.
In addition, the choice of welding process, whether it be MIG, TIG, or stick welding, must straighten with the specific requirements of the task to guarantee ideal outcomes. Appropriate cleansing and prep work of the base steel, as well as selecting the best filler material, are likewise necessary components of skilled welding strategies. By sticking to these ideal techniques, welders can decrease the threat of porosity development and generate high-quality, structurally sound welds.
Checking and Top Quality Control Procedures
Examining treatments are important to detect and protect against porosity in welding, making sure the strength and resilience of the final item. Non-destructive testing techniques such as ultrasonic testing, radiographic screening, and visual evaluation are generally utilized to recognize prospective issues like porosity.
Post-weld evaluations, on the other hand, evaluate the final weld for any defects, consisting of porosity, and validate that it satisfies specified standards. Implementing a comprehensive top quality control strategy that consists of complete testing procedures and examinations is extremely important to minimizing porosity problems and guaranteeing the overall top quality of welded joints.
Conclusion
Finally, porosity in welding can be a typical issue that affects the quality of welds. By recognizing the typical causes of porosity and applying finest practices for avoidance, such as proper welding strategies and testing measures, welders can make sure top quality and reliable welds. It why not try these out is necessary to focus on prevention approaches to reduce the event of porosity and preserve the honesty of welded frameworks.